Injection Mould Tooling in China: A Comprehensive Guide for Metal Fabricators
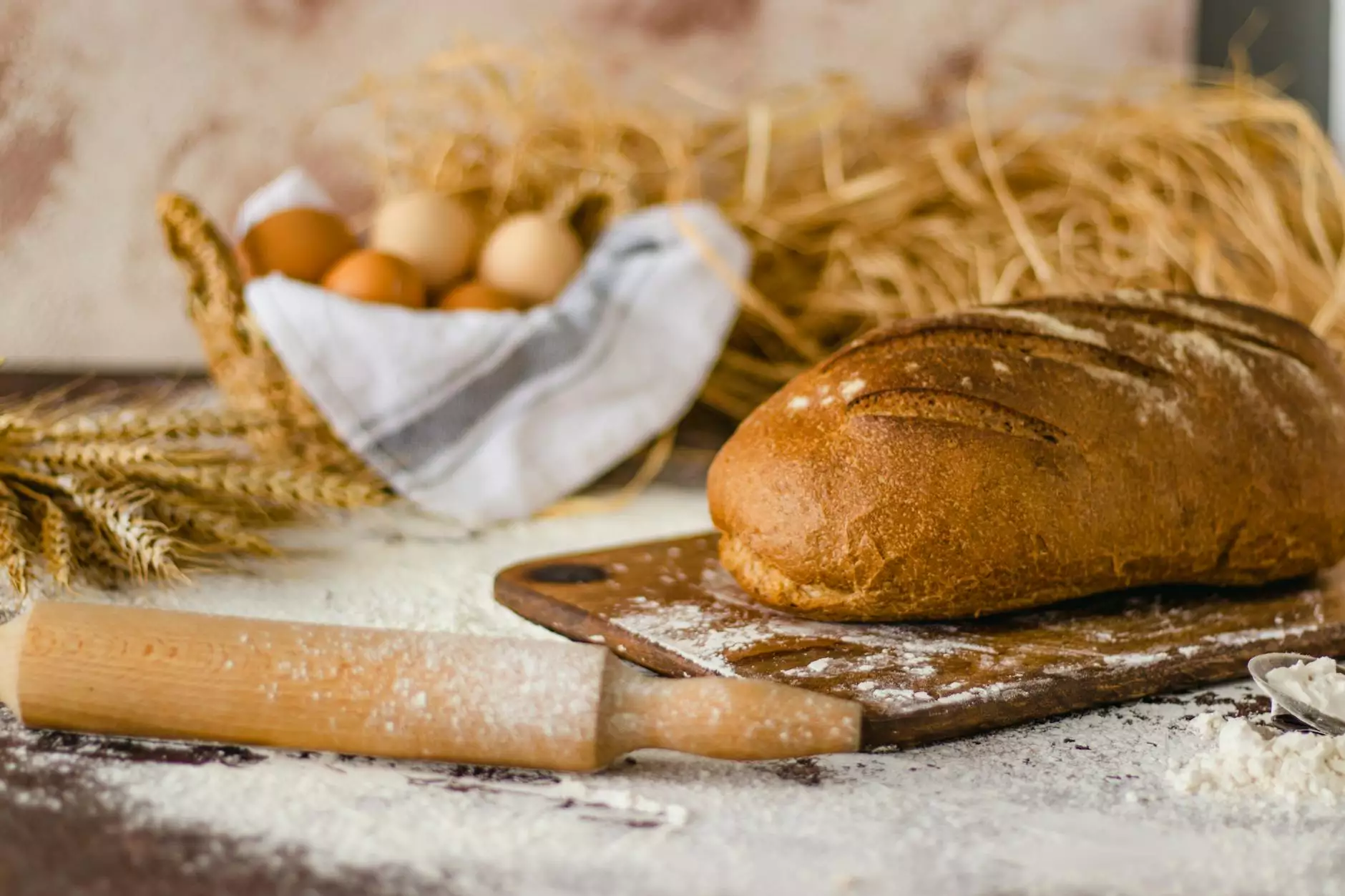
The world of manufacturing is ever-evolving, with innovation and efficiency taking the forefront. One of the most impactful advancements in this space is the specialization in injection mould tooling in China. This article aims to provide metal fabricators and businesses alike with a thorough understanding of the benefits, processes, and practical applications of injection mould tooling in this global manufacturing hub.
The Rise of Injection Mould Tooling in China
In recent years, China has emerged as a global leader in manufacturing, particularly in the field of injection mould tooling. The reasons behind this ascent are multifaceted:
- Cost-Effectiveness: Labor costs in China are significantly lower compared to Western countries, offering a financial advantage to manufacturers.
- Advanced Technology: Many Chinese factories are equipped with cutting-edge machinery and technology, enabling them to produce high-quality moulds.
- Skilled Workforce: Over the years, China has developed a highly skilled workforce that specializes in plastic injection moulding techniques.
- Efficient Supply Chains: Proximity to raw material suppliers and a robust logistics network contribute to quicker turnaround times.
Understanding Injection Mould Tooling
Injection mould tooling is a critical process used in manufacturing plastic parts. It involves creating a mould into which molten plastic is injected, allowing for the production of complex shapes and designs. Here’s a deeper look into this process:
Process Overview
- Design Phase: The process begins with a detailed design of the component, which may utilize CAD software to ensure precision.
- Mould Fabrication: Once a design is finalized, the mould is fabricated using high-quality materials, typically steel or aluminum, that can withstand high pressure and heat.
- Injection Phase: Molten plastic is injected into the mould under high pressure, filling the cavity and taking the shape of the mould.
- Cooling and Ejection: After the plastic cools and solidifies, the mould is opened, and the finished part is ejected.
Benefits of Using Injection Mould Tooling in China
The advantages of choosing injection mould tooling in China are numerous, particularly for metal fabricators looking to enhance their production capabilities:
1. Cost Savings
One of the primary reasons businesses opt for production in China is the substantial cost savings. The lower labor rates significantly reduce the overall production costs, allowing for competitive pricing in the market.
2. High-Quality Standards
Chinese manufacturers are increasingly adhering to international quality standards, ensuring that the products from injection mould tooling meet or exceed expectations. This commitment to quality is vital for businesses that require durable and reliable components.
3. Shorter Lead Times
With advancements in technology and a well-established supply chain, Chinese manufacturers can significantly shorten lead times. This ensures that metal fabricators receive their components on time, enabling quicker project turnarounds.
4. Flexibility and Customization
Injection mould tooling allows for greater flexibility in design, which is particularly beneficial for custom projects. Manufacturers can easily modify existing moulds or create new ones based on specific client needs, ensuring bespoke solutions for various applications.
Best Practices for Selecting a Mould Tooling Partner in China
Choosing the right partner for injection mould tooling in China is crucial for success. Here are best practices to consider:
1. Research and Compare
Conduct thorough research on potential manufacturing partners. Look for reviews, testimonials, and case studies that demonstrate their capabilities and reliability.
2. Assess Quality Control Measures
Inquire about quality control processes implemented within the production line. Certification in quality standards such as ISO 9001 can be a significant indicator of a company’s commitment to quality.
3. Evaluate Communication Channels
Clear and effective communication is essential. Ensure that your potential partner has a proficient English-speaking team that can facilitate smooth interactions.
4. Request Samples
Before making a commitment, request samples of previous work. This allows you to assess the quality and precision of their moulds directly.
Industries Benefiting from Injection Mould Tooling in China
Many industries are capitalizing on the advantages of injection mould tooling in China. Some of these industries include:
- Automotive: Injection-moulded parts are crucial for various automotive applications, including dashboards, panels, and connectors.
- Consumer Electronics: Moulded plastic components are foundational in creating devices like smartphones, laptops, and home appliances.
- Medical Devices: Precision and quality are paramount in the medical field. Injection mould tooling produces reliable components for various medical devices and equipment.
- Toys: The toy industry benefits from rapid production capabilities and custom designs made possible through injection mould tooling.
Challenges in Injection Mould Tooling in China
While there are many benefits, it’s also essential to consider potential challenges associated with injection mould tooling in China:
1. Intellectual Property Risks
Intellectual property theft is a concern when outsourcing manufacturing to China. Implementing strong legal agreements and working with reputable manufacturers can mitigate these risks.
2. Cultural Differences
Cultural misunderstandings can occur due to differences in business practices and communication styles. Establishing clear expectations and maintaining open lines of communication can help bridge these gaps.
3. Quality Variability
Not all manufacturers uphold the same quality standards. It’s essential to conduct due diligence and choose partners known for their reliability and quality assurance processes.
The Future of Injection Mould Tooling in China
The landscape for injection mould tooling in China is continuously evolving. With an increasing focus on automation and digital technology, we can expect significant advancements in precision, speed, and efficiency in the coming years. Emerging technologies such as 3D printing and robotic automation are likely to reshape traditional moulding processes, further enhancing China’s role as a leader in manufacturing.
Conclusion
In conclusion, the advantages of injection mould tooling in China are too significant to overlook for businesses seeking to optimize their production processes. By understanding the intricacies of this manufacturing method, weighing the benefits and challenges, and adopting best practices for selecting a partner, metal fabricators can leverage China's capabilities effectively. Embracing this aspect of manufacturing not only leads to cost savings but also fosters innovation and competitiveness in an increasingly globalized market.
For more information or to explore your options in injection mould tooling, visit DeepMould.net today!
injection mould tooling china