Maximizing Potential with a Plastic Injection Mold Tooling Factory
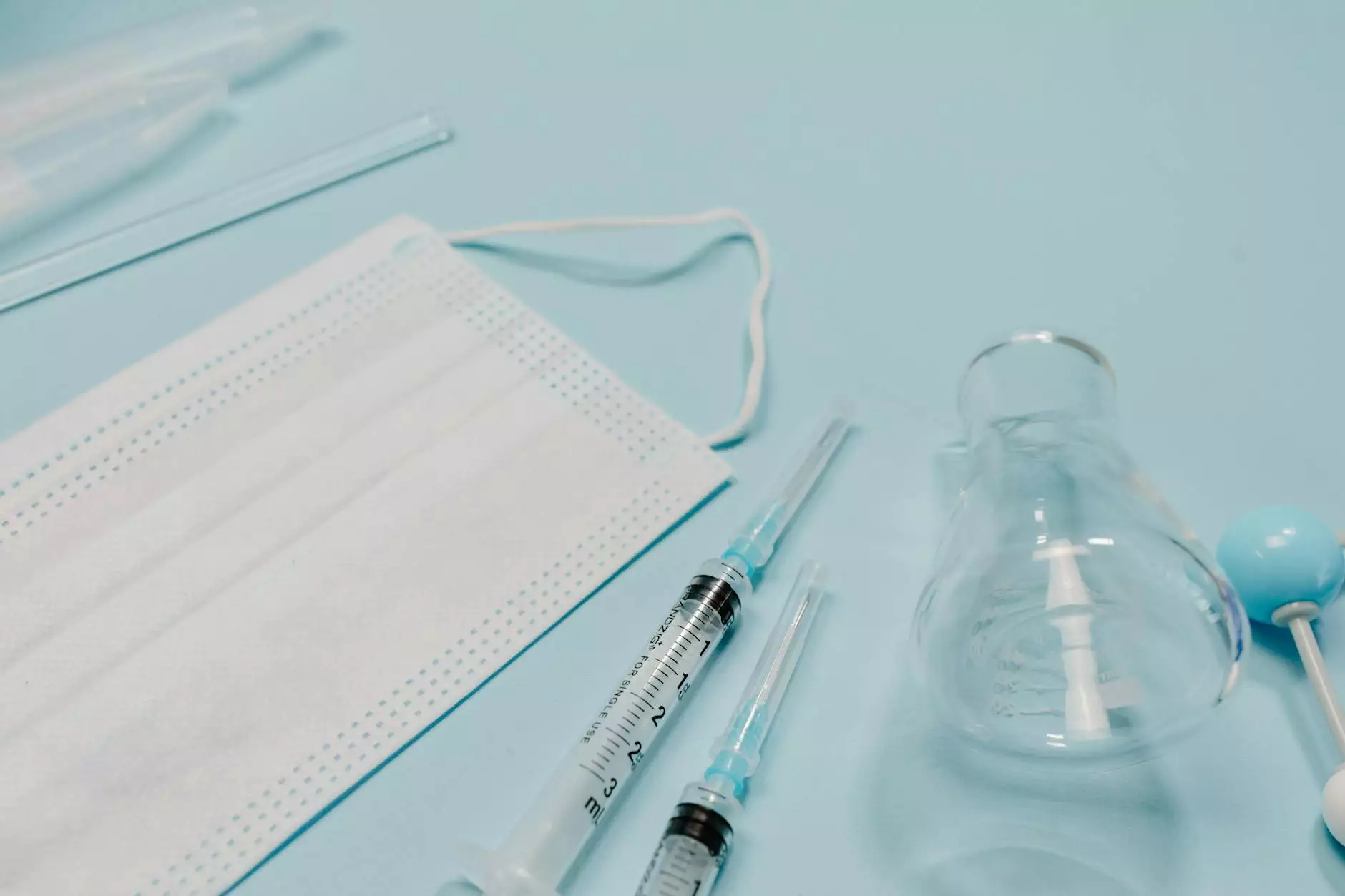
In today's fast-paced manufacturing landscape, businesses are continually seeking innovative solutions to enhance efficiency and productivity. A plastic injection mold tooling factory plays a pivotal role in achieving these goals, providing high-quality mold tooling solutions that meet the demands of various industries. This article delves into the multifaceted benefits of partnering with a specialized injection mold tooling factory and highlights how it can catalyze business growth and success.
The Significance of Plastic Injection Molding
Plastic injection molding is a highly efficient manufacturing process used for producing a wide range of plastic parts and products. It involves injecting molten plastic into a mold, where it cools and solidifies into the desired shape. The importance of this process in modern manufacturing cannot be overstated, as it offers numerous advantages:
- Cost-effectiveness: Large volume production significantly reduces the cost per unit.
- Precision: Injection molding allows for remarkable precision and repeatability in the production of intricate parts.
- Diverse Material Utilization: A variety of thermoplastics and thermosets can be used in the process.
- Minimal Waste: The process results in minimal material waste compared to other manufacturing methods.
Understanding Plastic Injection Mold Tooling
At the heart of any successful plastic injection mold tooling factory is the concept of mold tooling. Mold tooling refers to the creation of molds that are essential for the production of plastic parts. These molds are engineered with utmost precision to ensure they capture every detail of the design, allowing for seamless production. Here are some critical aspects of mold tooling:
- Materials Used: Common materials for molds include steel, aluminum, and specialty alloys, each chosen based on the application's specific requirements.
- Design Complexity: Advanced computer-aided design (CAD) software enables the design of intricate, complex molds that can produce highly detailed parts.
- Customization: Molds can be tailored to meet the unique specifications and demands of different products, ensuring flexibility in manufacturing.
Choosing the Right Plastic Injection Mold Tooling Factory
Selecting the right plastic injection mold tooling factory is crucial for achieving high-quality results and operational efficiency. Here are some factors to consider when making your choice:
- Experience and Expertise: Look for a factory with a proven track record and extensive experience in plastic injection molding.
- Technological Capabilities: Ensure the factory utilizes advanced technology and machinery to produce high-precision molds.
- Quality Assurance: A reputable factory will have robust quality control processes in place to ensure every mold meets industry standards.
- Customization Options: The ability to customize molds according to specific needs is essential for achieving the desired outcomes.
- Customer Support: Strong communication and support throughout the project can make a significant difference in the overall experience.
The Benefits of Partnering with a Plastic Injection Mold Tooling Factory
Collaborating with a specialized plastic injection mold tooling factory offers several advantages that can enhance your business operations:
1. Improved Time-to-Market
Working with an expert mold tooling factory streamlines the design and production processes, significantly improving your time-to-market. Fast turnaround times can provide a competitive edge, allowing businesses to respond to market demands more quickly.
2. Enhanced Product Quality
Quality is paramount in manufacturing. A skilled plastic injection mold tooling factory guarantees high-quality molds that lead to superior plastic parts. This enhances the overall product quality, which can lead to increased customer satisfaction and loyalty.
3. Cost Efficiency
By investing in high-quality mold tooling, businesses can reduce production costs in the long run. Quality molds require less maintenance, reduce wasted materials, and decrease the likelihood of defects, leading to significant savings.
4. Scalability
As your business grows, the need for scalable solutions becomes evident. A reliable plastic injection mold tooling factory can accommodate increased production needs, allowing businesses to scale operations smoothly without compromising quality or efficiency.
The Future of Plastic Injection Mold Tooling
As industries evolve, the process of plastic injection molding is also transforming. Innovations in technology, such as automation, 3D printing, and smart manufacturing, unlock new possibilities in mold design and production. Here’s a glimpse into what the future holds for plastic injection mold tooling:
- Automation: Increased automation will enhance efficiency, minimize human error, and further reduce production costs.
- 3D Printing: The integration of 3D printing technology in mold making can expedite the process and allow for more complex designs.
- Sustainability: Emphasis on eco-friendly materials and processes will shape the future, with the industry moving towards more sustainable practices.
Conclusion: The Path Forward with a Plastic Injection Mold Tooling Factory
In conclusion, a plastic injection mold tooling factory is an indispensable partner for businesses aiming to enhance their manufacturing capabilities. By leveraging the advantages of high-quality mold tooling, businesses can improve product quality, reduce costs, and accelerate their time-to-market. As you consider your options, remember to prioritize quality, experience, and innovation. The right partnership will not only drive your current operations but also set the foundation for future success in a competitive landscape.
For more information on how a plastic injection mold tooling factory can elevate your business, visit deepmould.net. Discover the comprehensive range of services and expertise that can help your business thrive in today's dynamic manufacturing environment.